Ajaokuta Steel Company is located on 24,000 hectares of sprawling green-field land-mass. The Steel Plant itself is built on 800-hectares of land. The chosen Technology for Steel Production is the time tested Blast-Furnace – Basic Oxygen Furnace route for Steel Production.

The Ajaokuta integrated steel complex was conceived and steadily developed with the vision of erecting a Metallurgical Process Plant cum Engineering Complex with other auxiliaries and facilities.
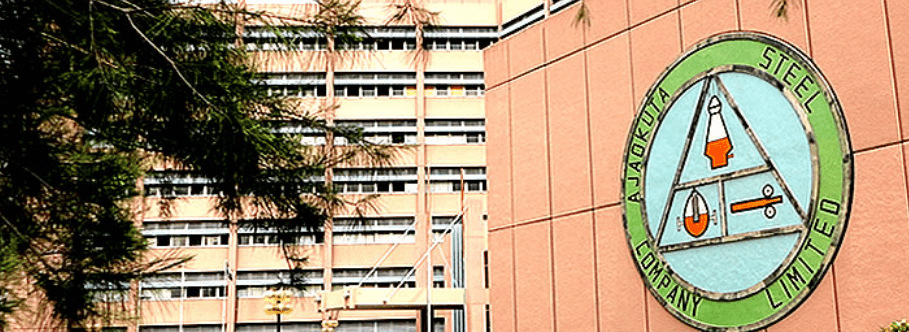
The Ajaokuta Steel Plant’s major units are as follows.
• Integrated Steel Plant based on BF- BOF Route
• Installed capacity – 1.3 Million Tonnes PA
• Provision to increase Capacity to 2.6 Million Tonnes and further to 5.2 Million Tonnes PA
• Rolling commenced November ’04
• Rolling Entire Range
• Wire rod 5.5 mm- 12 mm
• Rebars 8 mm – 30 mm
PLANT FACILITIES
• Coke Batteries – 0.88 MTPA capacity
• Sinter Plant – 2.6 MTPA of fluxed sinter
• Blast Furnace – 1.3 MTPA of hot metal.
• Two Basic Oxygen Furnaces – (130 tons each) 1.3 MTPA.
• Three continuous bloom casters of four strands each.
• Billet Mill – 795,000 TPA
• Wire Rod Mill (WRM) – 130,000 TPA
• Light Section Mill (LSM) – 400,000 TPA
• Medium Section and Structural Mills (MSSM) – 560,000 TPA
• Thermal Power Plant can produce a total of 110 MW from 2 generators of 55MW each.
Among the auxiliary plants are the
• Lime Production Plant,
• Alumino Silicate Refactory Plant and
• Tar bonded Dolomite Plant.
These major units are serviced by an array of water treatment and recirculation facilities and extensive gas facilities. A captive Power Plant of capacity 110mw is to provide an alternative source of power to the Steel Plant.
Engineering Complex:
Engineering Complex as one of the auxiliary units adequately equipped with machines and equipment for the manufacture of spare parts and fixtures of various specifications.
CAPABILITY
• Billets
• 100 x 100 mm
• WRM
• Wire rods of size between 5.5 mm to 12.5 mm.
• Re bars of size between 6.0 mm to 12 mm.
• LSM
• Plain and re bars : 10 mm to 30 mm
• Squares : 10 mm to 30 mm.
• Hexagons : 10 – 14 mm , 20 and 26.
• Angles : 25×25 mm to 50×50 mm in thickness between 3 mm to 6mm.
• Channels : 30 mm to 45 mm.
• T – sections : 30 mm to 60 mm.
• Strips : 6-12 ( t ) x 12 – 70 ( w )mm
• MSSM
• I beams : 80 mm to 300 mm.
• Channels : 80 mm to 300 mm.
• Equal angles : 70 x 70 mm up to130x130 mm.
• Un equal angles. : 50×80 mm and 100 x 160 mm.
• Flats : 70 mm to 150 mm width x 10 to 20 mm in thickness.
The steel plant is meant to be used to generate important upstream and downstream industrial and economic activities that are critical to the diversification of our economy into an industrial one. Ajaokuta Steel Plant is therefore aptly tagged as the “Bedrock of Nigeria’s industrialization”
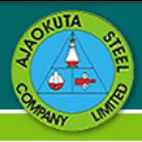
The Federal Government of Nigeria established the Nigerian Steel Development Authority (NSDA) in 1971 through Decree No. 19 in order to advance the development of the Nigerian Steel Industry. NSDA carried out detailed market studies and investigations on local availability of raw materials.

The Preliminary Project Report (PPR) of 1974, the Detailed Project Report (DPR) of 1977 and the Global Contract (1979) for construction of steel plant at Ajaokuta were all commissioned and executed during the NSDA period.

The NSDA was thereafter dissolved through decree No. 60 on the 18th of September 1979. This decree also created Ajaokuta Steel Company Limited, ASCL being the successor of NSDA.
The project was embarked upon as a strategic industry, a job creator and a foreign exchange saver and earner.

It was envisaged that the project would generate a myriad of socio-economic benefits and increase the productive capacity of the nation through its linkages to other industrial sectors.

It would provide materials for infrastructural development, technology acquisition, human capacity building, income distribution, regional development and employment generation.

While the project would directly employ about 10,000 staff at the first phase of commissioning, the upstream and downstream industries that will evolve all over the nation will engage not less than 500,000 employees.
The plant by 1994 was reckoned to be at 98% completion in terms of equipment erected. Some completed units of the Plant operated at different times but had to short down due to non-availability of fund.