The hot metal car, often referred to as a torpedo car, played a crucial role in the steel manufacturing process, revolutionizing the transportation of molten iron from blast furnaces to steel mills. With its specialized design, durability, and remarkable efficiency, it became a hallmark of the industrial age.
The Ingenious Design of the Hot Metal Car
The hot metal car was engineered for one purpose: safely and efficiently transporting molten iron at extreme temperatures. The firebrick-lined cylinder, a pivotal feature of the car, provided exceptional insulation, allowing the iron to remain in its liquid state for up to 24 hours. This capability was essential for large-scale steel production, as it prevented cooling and solidification during transit.
Key Features:
- Thick Metal Plate: Withstood immense heat and the weight of molten iron.
- Firebrick-Lined Cylinder: Ensured thermal insulation for prolonged periods.
- Hatch Design: A small opening at the top facilitated safe pouring of liquid iron.
- Bottlelike Shape: Optimized weight distribution and heat retention.
Size Variations:
- Standard Cars: Typically had 12 wheels and weighed up to 125 tons when fully loaded.
- Larger Units: Boasted 16 wheels and could weigh as much as 400 tons.
Bethlehem Steel Company (BSCo) No. 127: A Mid-Sized Workhorse
One of the most iconic examples of hot metal cars was the Bethlehem Steel Company No. 127, a mid-sized model that epitomized efficiency and durability. Built circa 1935 by the M.H. Treadwell Company, this car was among 54 similar units that serviced Bethlehem Steel’s sprawling facility at Sparrow’s Point, Maryland.
Historical Significance:
- Active Years: Operated until 1977, marking over four decades of service.
- Retirement and Preservation: Donated to the B&O Railroad Museum in 1984, it arrived in 1997, preserving its legacy as an industrial artifact.
The Decline of the American Steel Industry
While the hot metal car symbolized industrial ingenuity, its decline mirrored the challenges faced by the American steel industry. The 1970s and 1980s witnessed a steep downturn due to factors like global competition, outdated facilities, and economic shifts. This downturn culminated in the closure of iconic companies such as Bethlehem Steel, which ceased operations in 2003.
Key Milestones:
- 1969: M.H. Treadwell facility was acquired by Bethlehem Steel.
- 1970s–1980s: Industry collapse led to reduced production and workforce downsizing.
- 2003: Final closure of Bethlehem Steel, marking the end of an era.
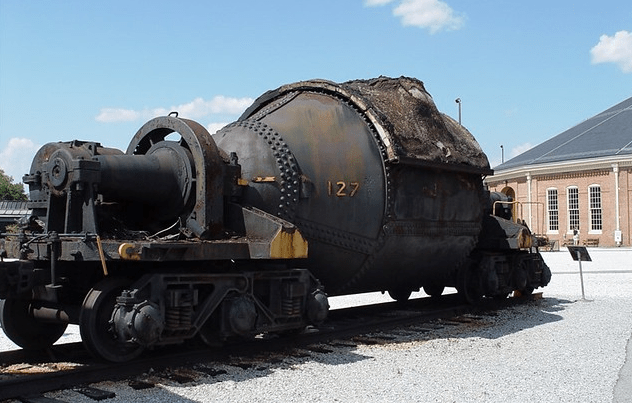
Cultural and Industrial Legacy
The Bethlehem Steel Company No. 127 stands as more than just a piece of industrial equipment—it’s a symbol of Maryland’s industrial heritage and the broader story of American manufacturing. Preserved at the B&O Railroad Museum, it offers a tangible connection to a time when steel production powered the nation’s economy.
The hot metal car, with its robust design and crucial function, remains a testament to the innovation and resilience of industrial engineering. Its story, intertwined with the rise and fall of the American steel industry, continues to inspire a deeper understanding of our industrial past.